Company-wide-training per Italian Wine Brand
Presentiamo ora un caso di successo di un grande piano di formazione che ha contributo a riportare uno dei maggiori gruppi vinicoli italiani, quotati in borsa, alla redditività e a razionalizzare i propri processi rendendoli più efficienti.
Realizzare la Complete Lean Transformation significa trasformare con approccio scientifico SPDCA (Scan, Plan, Do, Check, Act) le 4D (Delivery, Demand, Development, Deployment) dell’organizzazione. Vuol dire portare l’approccio Lean a livello di una cultura manageriale che definisca le strategie, le renda coerenti tra di loro e, soprattutto, conduca ad allineare l’intera organizzazione e l’insieme delle attività che questa sta compiendo.
Il processo di trasformazione prevede la definizione e il raggiungimento di obiettivi in accordo con i cinque principi fondanti della Lean:
Principio 1: valore percepito dal cliente (Value Analysis);
Principio 2: flusso del valore (Value Stream Mapping);
Principio 3: flusso continuo di produzione (One-piece-flow);
Principio 4: “Pull”;
Principio 5: “Kaizen” (eccellenza).
Attività.
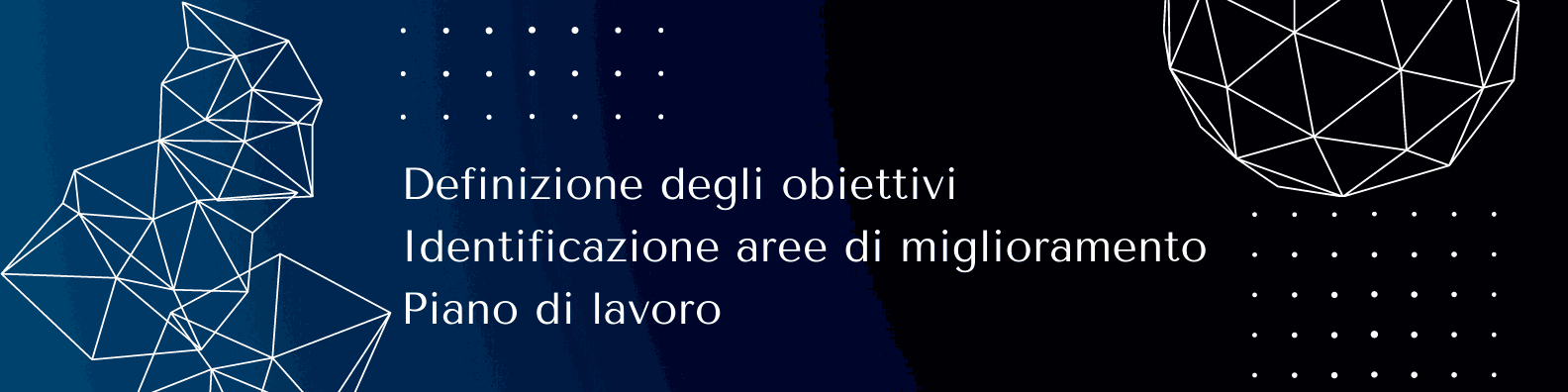
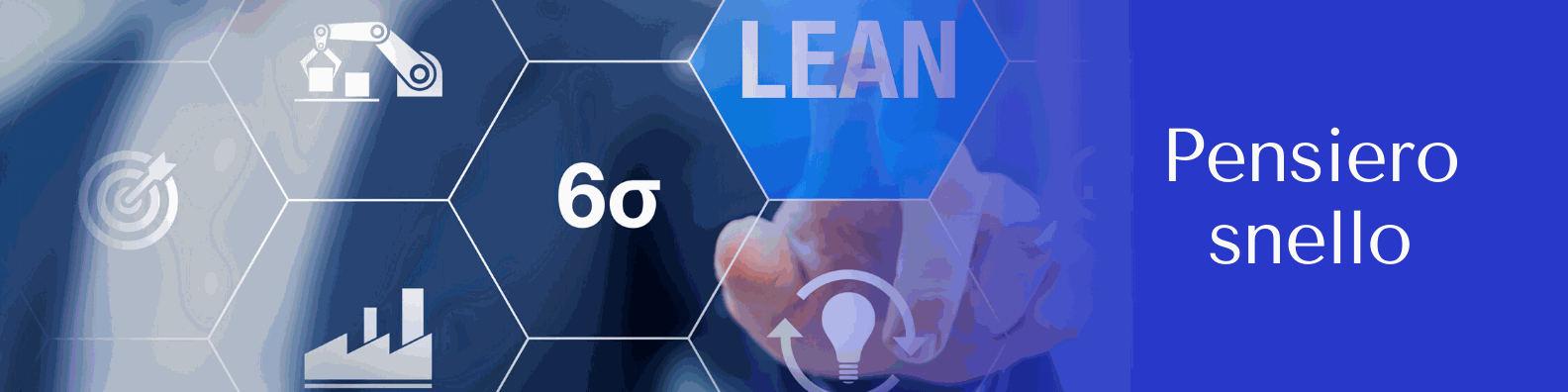
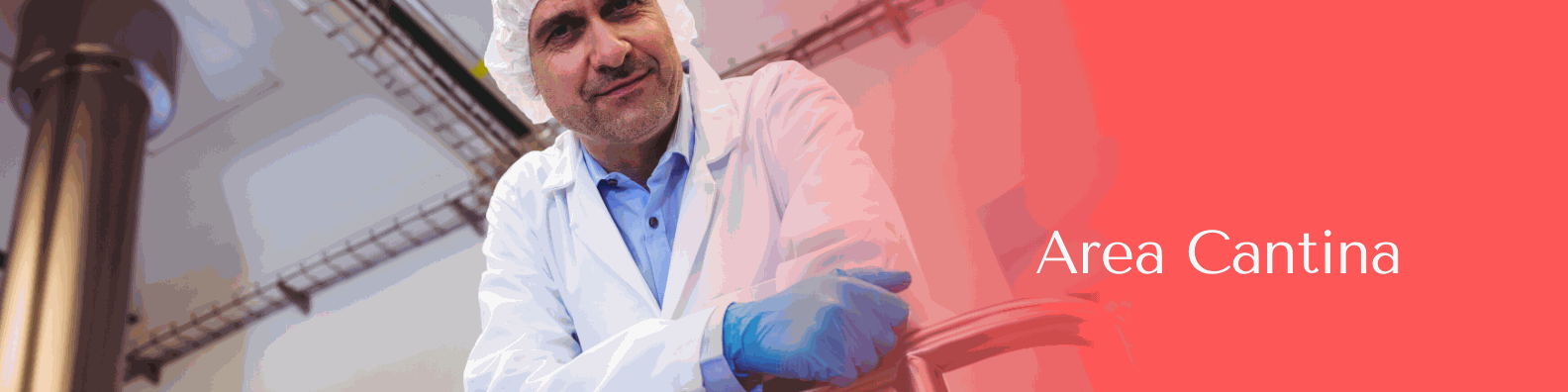
Area cantina.
Just In Time;
Lay-out e Bilanciamento della linea;
Flessibilità mediante operatori polivalenti (Shojinka);
Heijunka: livellamento del volume e del mix di produzione;
Mixed model line;
Le matrici di cambio formato per ridurre i tempi di set-up;
La Group Technology nei magazzini;
KANBAN (mettere “in tiro” il flusso logistico);
Tipologie di Kanban, regole, vantaggi;
Implementazione di un magazzino di disaccoppiamento KanBan.
Area imbottigliamento.
• Analisi del Takt Time per definire il ritmo della produzione;
• TPM, Total Productive Maintenance;
• Eliminare le sei grandi perdite;
• OEE Overall Equipment Effectiveness;
• Misurare le perdite (MTBF, MDT, MTTR, ..)
• Strumenti di analisi (Diagramma di Ishikawa, i cinque perché);
• La manutenzione autonoma: passi fondamentali, consigli;
• SMED (Single Minute Exchange of Die) per ridurre i tempi di set-up;
• Realizzazione di un cantiere SMED.
Area magazzino, confezionamento.
Just In Time;
Lay-out e Bilanciamento della linea;
Flessibilità mediante operatori polivalenti (Shojinka);
Heijunka: livellamento del volume e del mix di produzione;
Mixed model line;
Le matrici di cambio formato per ridurre i tempi di set-up;
La Group Technology nei magazzini;
KANBAN (mettere “in tiro” il flusso logistico);
Tipologie di Kanban, regole, vantaggi;
Implementazione di un magazzino di disaccoppiamento KanBan.